Microfabrication Lab Project Report:
A Simple CMOS Pressure Sensor
R. Timothy Edwards
December, 1994
Abstract-In a clean room that isn't especially clean,
in a crowded environment with mostly hand-me-down and often
faulty equipment, and in the
face of great odds, we actually fabricated a real, working
pressure sensor. What more could we ask for?
Disclaimer-This paper describes a course in the Electrical
and Computer Engineering Department of Johns Hopkins University
Whiting School of Engineering. The lab is intended to give students
hands-on experience with chip fabrication. It is not a commercial
fab line, and its capabilities are behind the state-of-the-art by
at least twenty years, being composed of second-hand equipment,
much of which dates back that far. This online paper is intended
to give interested students and others a feel for what the course
is about, and for what can be accomplished with such a setup.
For More Information-Every now and then I receive email
from people interested in detailed information about the microfabrication
laboratory. I am not especially qualified to answer such questions,
but I would suggest contacting the laboratory TAs or the course instructor.
They are as follows:
Introduction
Microfabricated pressure sensors comprise a small but useful subset
of integrated circuits. Integrated sensors of high quality can be
very sensitive to pressure changes, making them ideal for applications
in which bulky machined sensors are not able to perform, or are too
large, or consume too much power.
Typical applications of integrated pressure sensors include microphones,
biomedical instrumentation ( e.g., blood and fluid pressure),
vacuum sensing, wind-tunnel model instrumentation, automobile power
and acceleration measurement, and even household electronics
[3].
There are a number of ways to go about designing and building an
integrated sensor. The most common and inexpensive type, which is
the type built for this project, is based on the piezoresistive
effect, which is described in detail below. Piezoresitors can
be made of doped silicon or polysilicon. Polysilicon has better
stability, avoids time- and temperature-variant p-n junctions,
and can be used in operating temperatures up to 200°C [1].
All mechanical
sensors are based on material changes caused by stress placed
on a membrane or other flexible element. On the submillimeter
scale of integrated devices, materials like silicon show very
little or no fatigue, which is apparently a macroscale phenomenon.
Thus integrated sensors can be flexed indefinitely, and have a long
lifetime.
In addition to sensors based on the piezoresistive effect,
there also exist high-precision sensors based on capacitive
effect. A membrane is also used, with one plate of a capacitor
mounted on the membrane and the other plate suspended above it, usually
fabricated on a relatively inflexible material such as Pyrex glass.
The deflection of the membrane changes the distance between the
plates and thus changes the capacitance. Capacitors tend to be
much less temperature and time variant than piezoresistors. Output
of capacitive sensors is highly appropriate for switched-cap circuit
design [2].
Other mechanical sensors are based on micromachining techniques.
Silicon reed oscillators are formed from a millimeter-scale paddle
suspended by a thin silicon bridge, which is caused to oscillate.
The amplitude of the vibrations are highly sensitive to pressure
changes, and make a good sensor for measuring vacuums in the
10e-2 to 10e5 Pa range. Another kind of vacuum sensor is
made from a micromachined floating membrane [1].
When standard
or modified CMOS or bipolar processes are used in order to fabricate
the sensor, signal processing can be done at the source.
On-chip amplification of the signal is the first necessary step
to ensure minimizing the effect of noise on the output. On-chip
circuitry is also necessary in a high-quality system to compensate
for temperature variation.
Temperature-dependent behavior is seen as the limiting factor
in integrated sensors. Bandgap reference circuits are designed
which have a negative temperature coefficient. This is added to
the output to compensate for the positive temperature coefficient
of the sensor. The voltage reference can either be designed by
circuit and material analysis to compensate for the expected
temperature dependence of the sensor, or it can be made programmable
and the chip can be calibrated after manufacturing. High-performance
systems often have bandgap references which are tuned after
manufacture by laser trimming [1]. This of course
adds to the cost of the device.
Early digitization of the signal is another common treatment which
eliminates the problem of noise and
nonlinear effects between the sensor and the instrument or control
system that depends on its output. An alternative to digital output
is a frequency-based output such as duty-cycle variation which is
also robust in the presence of noise.
Piezoresistive Sensors
Certain materials, of which Silicon is a notable example,
are sensitive to changes resulting from stress applied to the
crystal lattice. Resistance, in particular, is dependent on
the changes in length caused by stress. Resistive changes are
not isotropic, and can be divided into two independent functions,
one component parallel to the direction of stress, and one component
perpendicular to it, in the form of:
where
and
are the perpendicular
and parallel components of stress, respectively, and
and
are the
perpendicular and parallel piezoresistive
coefficients. The coefficients are functions of temperature and
doping concentration. The stresses are proportional to pressure
and to the the square of the ratio
/ h
where h is the thickness of the membrane and
is the distance from the membrane center to the edge [5].
Sensors are sometimes designed using finite element analysis or
other precision simulation to find membrane and resistor shapes
and configurations which maximize this sensitivity.
About the simplest sensor circuit that can be built using piezoresistors
is the Wheatstone bridge, shown below.
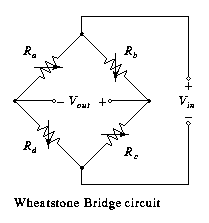
The bridge is made of four piezoresistors
located on the four edges of the sensor membrane, close to the edges where the
stress is greatest when vertical pressure is applied to the center (or uniformly
across) the membrane. Two of the resistors are positioned parallel to the
direction of the stress, and their resistance increases with pressure. The
other two resistors are oriented perpendicual to the direction of the stress,
and their resistance decreases with pressure. This configuration is shown in
the figure below. The parallel resistors are made as two resistors in series in
order to maximize sensitvity, which is a decreasing function of distance
from the edge of the membrane, while keeping the absolute resistance
the same as the perpendicularly-oriented resistors.

Configuration of piezoresistors around a membrane.
The solution to the Wheatstone bridge as shown in the schematic above is:
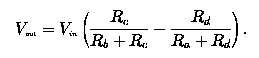
Resistors
and
are oriented parallel to the stress, and resistors
and
are oriented
perpendicular to it. Thus when the resistance of
increases and
decreases,
the output increases. This is the configuration of our
fabricated sensor, with the resistor ends leading to bonding pads.
Configuration of the bridge and signal amplification are all off-chip, to
reduce the number of steps in the process and make is feasible for the
project to be completed by untrained students in one semester.
Fabrication Process
The figure at the top of the paper shows the layout of one sensor device
on our chip. Mask layers (see below) are as follows:
- (Green) p-diffusion
- (Red) back-etch
- (Black) contact cuts
- (Blue) aluminum
The fabrication process begins with a 4'' wafer of about 400µm thickness,
n-type, <100> orientation. The process steps are outlined and
illustrated below.
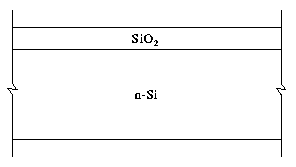
A layer of oxide is built by wet oxidation in a furnace at 1100°C
for 60 minutes.
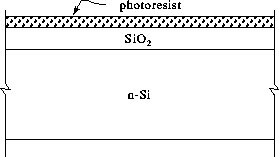
3 ml OCG 820 27CS photoresist is spun on at
4000 rpm for 60 s, and prebaked at 110°C for 45 s.
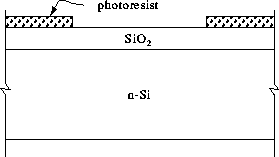
Wafer is aligned to mask 1, exposed for 12 seconds, and developed
for 20 seconds in a developer solution of 4:1 H2O and OCG developer
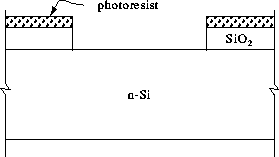
Diffusion openings are etched into the oxide by immersion in an
etchant (296 g NH4F, 106 ml HF, and 425
ml DI water) for 5 minutes.
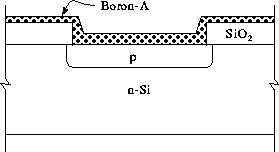
3 ml Boron-A dopant is spun on for 60 seconds at 3000 RPM and
maximum acceleration, then diffused in a furnace at 1100°C
for 60 minutes in a nitrogen atmosphere.
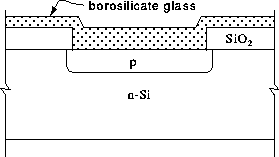
Steam is introduced into the furnace, and forms a layer of
borosilicate glass on the surface. Glass is grown for 40 minutes
at 1100°C.
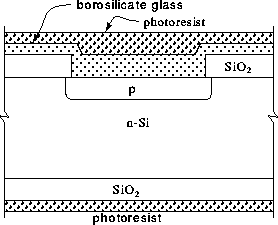
Wafer is baked at 200°C for 30 minutes. Photoresist
is then applied to the front side of the wafer for protection,
spun on at 4000 RPM for 60 seconds, and hard-baked at 150°C
for 30 minutes. Next, photoresist is spun onto the backside of the
wafer at 3000 RPM for 60 seconds, and prebaked at 110°C
for 45 seconds.
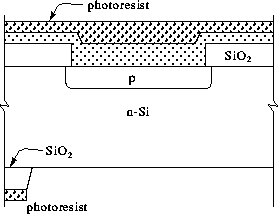
Wafer is aligned to mask 2 (on the backside), exposed for 15
seconds, and developed for 15 seconds in 1:4 KTI 809 developer and
DI water. Wafer is postbaked at 130°C for 60 seconds.
Oxide is etched from backside by immersion in buffered HF for 5
minutes.
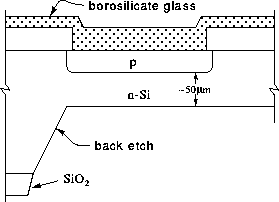
Photoresist is stripped off with acetone. Si is etched from
backside in KOH solution at 60°C, until thickness of
membrane is about 50 µm.
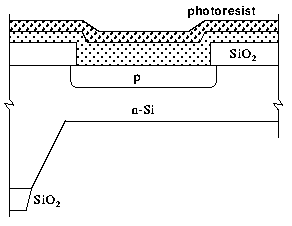
Photoresist is applied to front side at 4000 RPM for 60 seconds,
and prebaked at 110°C for 45 seconds.
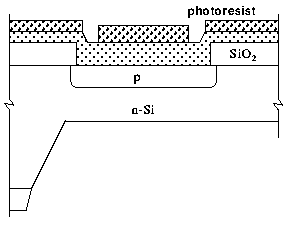
Wafer is aligned to mask 3, exposed for 15 seconds and developed
for 15 seconds in 1:4 KTI 809 deveoper and DI water. Wafer is postbaked
at 130°C for 60 seconds.
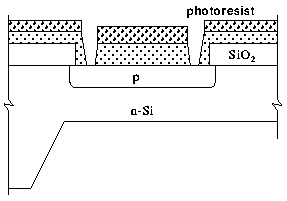
Wafer is etched in buffered HF for 5 (?) minutes until oxide and
borosilicate glass are removed from the contact cuts.
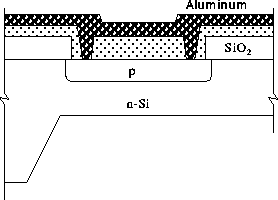
Aluminum is evaporated onto the front side of the wafer. In our
setup, 0.5 g of Aluminum wire was evaporated in a chamber at
approximately 8e-7 torr. This created a layer of
about 4.5 µm thickness.
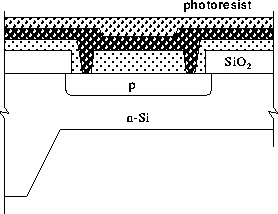
Photoresist is spun on at 4000 RPM for 60 seconds, and prebaked
at 115°C for 60 seconds.
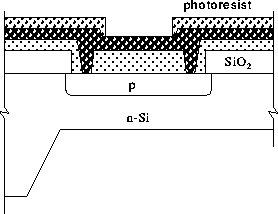
Wafer is aligned to mask 4, exposed for 15 seconds, developed for
12 seconds in
1:4 KTI 809 developer and DI water, then postbaked at 130°C
for 60 seconds.
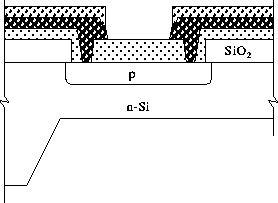
Aluminum is etched by immersion in PAN etch (75 ml phosphoric
acid, 3 ml nitric acid, 15 ml, and 5 ml DI water) for
approximately 10 minutes, until aluminum is visibly removed.
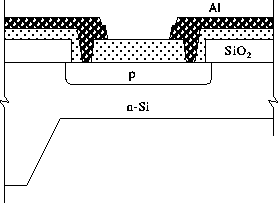
Photoresist is removed with acetone, then annealed at 450°C
in a nitrogen atmosphere for 30 minutes.
Fabrication is completed by scribing and dicing the wafer, mounting on a copper-plated
printed circuit board with epoxy, and bonding the pads to the bond fingers.
Results
Physical structures on the chip were measured during the course of processing:
- Membrane thickness: 67 µm
- Aluminum thickness: 0.44 µm
Electical structures were measured upon completion of the chip but before scribing
and dicing:
- Large p-diffusion test resistor: 1.266 k
- Large resistor chain: 0.5 k
There was a high variation in resistance values across the chip. For the
four piezoresistors surrounding the membranes, the mean value was
144
.
The average standard deviation for resistors around the same membrane was
2.56
,
but the standard deviation for all resistors was
11.86
.
Test structures on the chip were analyzed with the following results:
- Diffusion sheet resistance:
12.84
/
.
- Metal sheet resistance:
0.34
/
.
- Sensitivity: 9.4 µV/V-mmHg.
-
Piezoresistors had the following values:
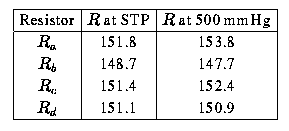
The response of the system was measured by amplifying the output of the
Wheatstone bridge with a simple amplifier circuit constructed out of a
1NA101-AM Burr-Brown integrated amplifier, using an external resistor
of 400
to provide a gain of approximately 100.
Input was
2.32 V AC at about 100 Hz. Output was measured with the back of the
mounted chip attached to a vacuum pump capable of pressures in the range
50-500 mmHg. Settling time of the response was quite large, possibly
due to the unconnected substrate (which was possibly connected to all of
the resistors through the contacts, which had an extreme amount of
undercut due to overetching), and probably also due to temperature
effects at the resistors heat and cool in response to current flow
in the circuit. Measurements are not entirely accurate
due to the impatience of the observer. Measurements tended to be lower
when read as the vacuum pressure was lowered from 500 mmHg to zero,
and higher when read as the vacuum pressure was raised from zero to
500 mmHg. Due to this and the jitter of the vacuum pump, no attempt
will be made to assess the linearity of the system, other than to
note that it looks reasonable.
Output AC voltage of the system was measured with a Keithly multimeter.
The amplifier frequency response was measured in the context of the
entire system and had a bandwidth of 30 kHz.
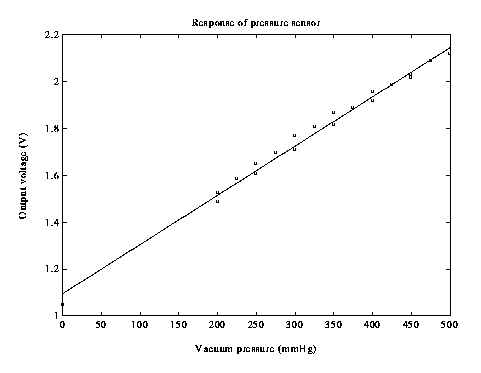
Response of system with gain of 100.
Discussion
This little chip was clearly not intended to compete with state-of-the-art
devices. It has no temperature compensation, has low sensitivity, and
rather low yield. However, I will make some attempt to compare it
to a capacitive sensor built by F. V. Schnatz et al in
Germany in 1991 and presented at the 6th International Conference on
Solid-State Sensors and Actuators, San Francisco, June 24-28, 1991
[2].
The capacitive pressure sensor is built with a standard CMOS 3 µm
n-well process. This is a useful property since the chip can be sent
off to any high-quality commercial or institutional lab and postprocessed
to create the membrane (obviously the point of our lab was to be
hands-on through the entire process). For feature-size comparison, our
smallest features were on a 20 µm scale.
The capacitive sensor features a membrane ``bossed'' on the underside,
which means the membrane itself forms a square, with the middle of
the membrane being the same thickness as the rest of the wafer. This
increases linearity of the capacitor by ensuring that the capacitive
plates, which are situated over the boss, are flat and move without
bending relative to the top plate.
The top plate is formed on Pyrex glass etched to form support columns
to hold the capacitor top plate at the proper distance from the bottom.
The metal top plate is deposited directly onto the glass, and the
glass structure is bonded anodically to the chip.
Chip circuitry features a programmable voltage reference and a
switched-cap amplifier. Output is a voltage, which makes it easier
to compare the performance to that of our chip.
The standard CMOS process involves about 7 or 8 mask steps, and
the chip requires one additional mask to define the bossed
membrane, and two mask steps are required to etch and metallize
the Pyrex glass. This is a total of at least 10 masks for
fabrication, compared to our four masks.
Nonlinearity of the chip output voltage was confined to 0.4%
over the operating
range of 0 to 30 kPa, with an output of 1.0 V to 5.0 V over
that range. Note that we did not attempt to find an upper
limit of pressure for our sensor, but it is doubtful that it
should be operated much above our test limit of 500 Pa. The
capacitor pressure sensor therefore has an operating range which
is orders of magnitude larger than that of our chip.
Sensitivity for the capacitive sensor is measured as change in
capacitance per unit pressure. The capacitor has
temperature-dependent offsets and sensitivity which, although
not as severe as temperature dependencies in a resistor, can
be reduced by the bandgap reference circuit. Due to limited
time and equipment, I did not attempt to characterize the
temperature dependence of our circuit.
Conclusions
The experience of having fabricated a working circuit in silicon
is a wonderful thing in and of itself, and
that a working circuit was the end result of this laboratory is
all the conclusion that is required here.
I have very few recommendations for future work; a few things
are obvious necessities such as a substrate contact somewhere on
the chip, and remaking the mask for which there were no large-scale
alignment bars. If the knowledge and experience gained from this
year makes next year's project run smoother and faster, then it
would probably be well worth the while to add a passivation layer
and an extra mask step for contact cuts. It would also be helpful
if a better method existed for aligning the back side of the wafer
to the front, although it appears that I was the only person to
suffer a serious misalignment problem, the source of which is
not known to me. One problem with misalignment of the back is
that it is virtually impossible to detect the misalignment until
the chip is diced up.
Acknowledgements
I would like to thank Dr. Norman Sheppard, Dr. Andreas Andreou, and
Robert Greenberg for their unceasing efforts in making this an
efficient and educational fabrication laboratory.
Bibliography
[1] Hauptmann, Peter. Sensors: Principles & Applications ,
Hertfordshire, UK, Carl Hanser Verlag (1991).
[2] F. V. Schnatz et al. ``Smart CMOS capacitive pressure
transducer with on-chip calibration capability,'' Sensors &
Actuators A (Physical) , Vol. 34, July 1992, pp. 77-82.
[3] Moon Key Lee, Bo Na Lee, and Seung Min Jung, ``A bipolar
integrated silicon pressure sensor,'' Sensors & Actuators A
(Physical), Vol. 34, July 1992, pp. 1-6.
[4] Jaeger, Richard C. Introduction to Microelectronic
Fabrication, Reading, MA, Addison-Wesley (1993).
[5] S. Clark, and Kensall Wise, ``Pressure sensitivity in
anisotropically etched thin-diaphragm pressure sensors,''
IEEE Transactions on Electron Devices , Vol. ED-26, No. 12,
December 1979, pp. 1887-1896.
Hardcopy (PostScript) of this project report: sensor.ps
Back to my home page. . .

email:
|
|